professional projects
projects made during time as an intern and mechanical engineer
The photos and descriptions below are for evaluation only and should not be distributed.
HYDRAULIC SAFTEY BRAKE
~2022~
Designed a hydraulic brake using a cylinder and custom manifold to slow the descent of a scissor lift. The effort was made to ensure user safety if the main hydraulic system failed by greatly slowing the descent of the lift.
The manifolds and reservoirs were designed to be machined in house out of aluminum. Various hydraulic cartridges were installed to slow or stop descent in some cases. Hard line hydraulic tubing was designed to integrate into a dynamic upper assembly.
The system was rigorously tested in many different cases and has been installed in a mechanically complete product.

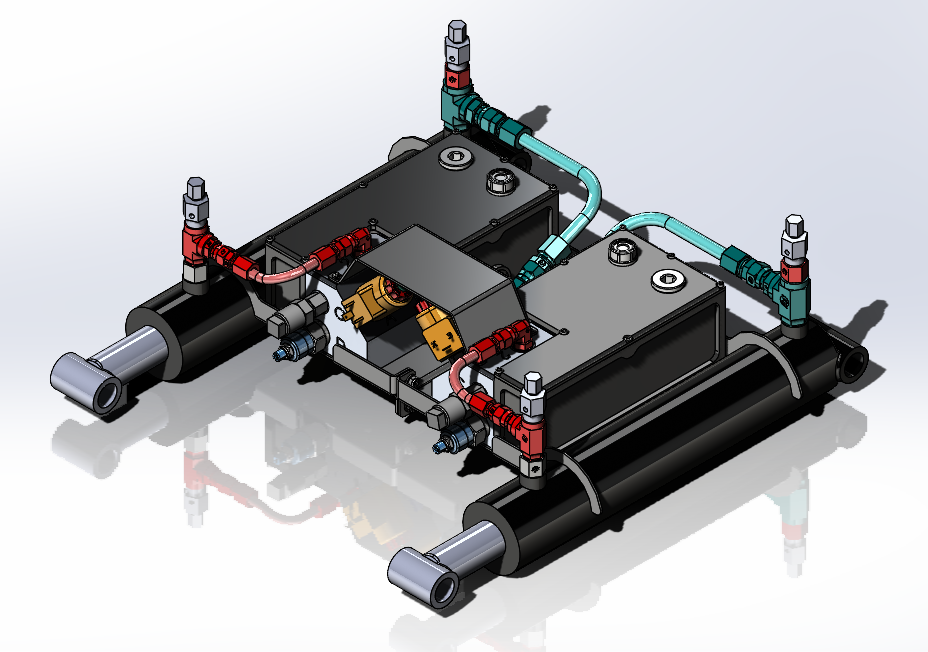
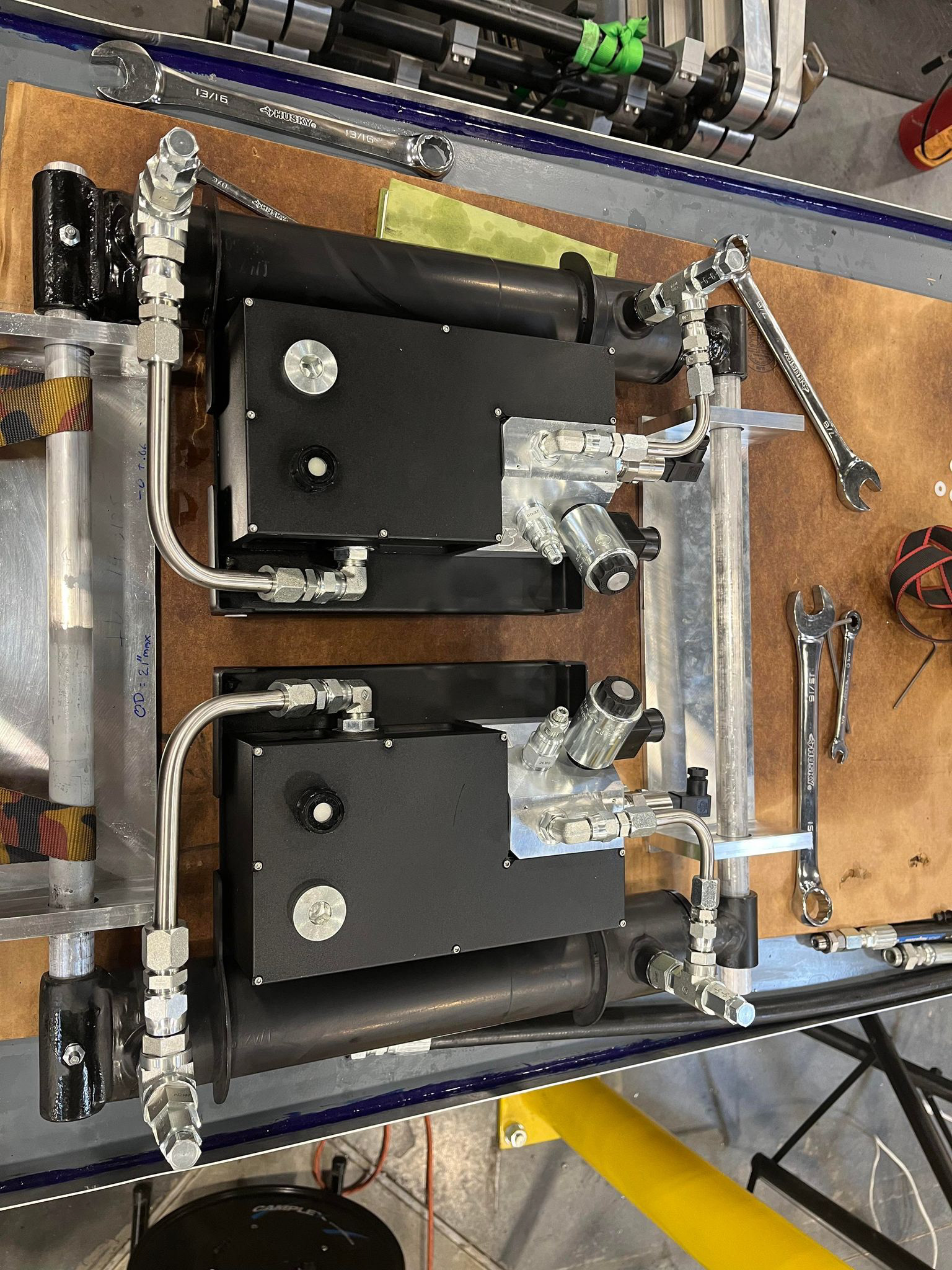
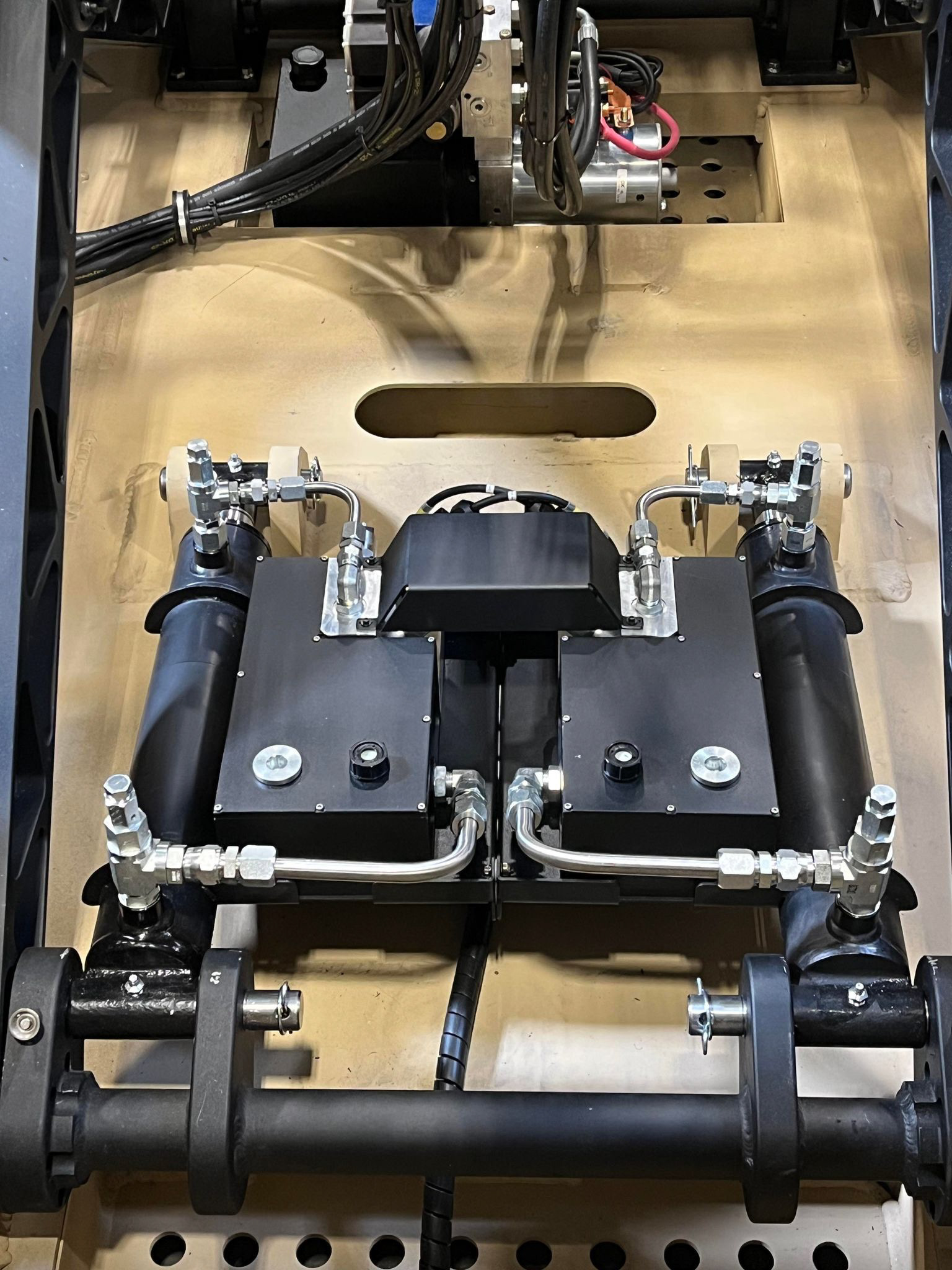
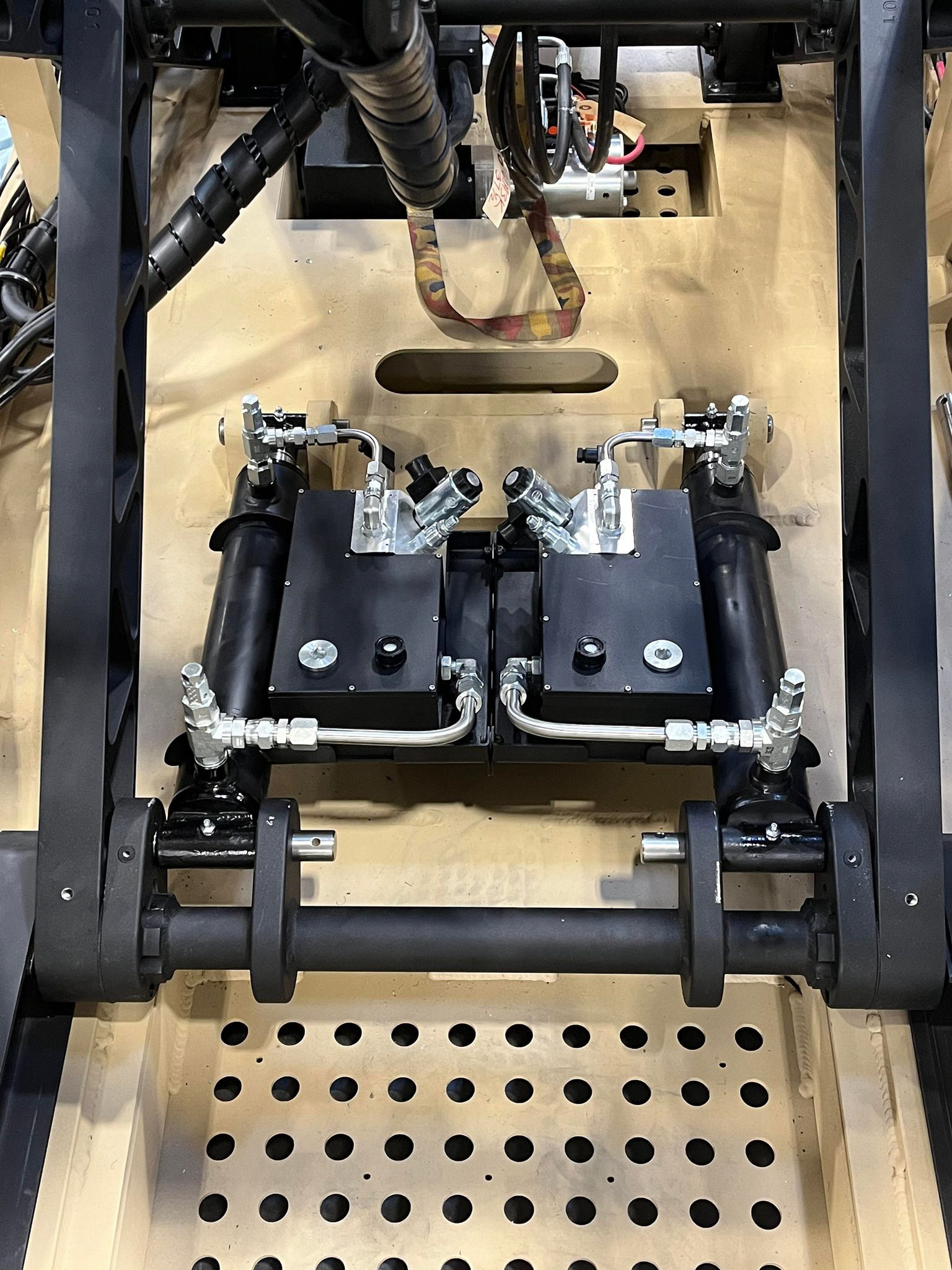
ANTENNA MOUNT
~2022~
Designed a mount for an antenna that allowed users to easily deploy and un-deploy the unit with ease. The mount was attached to a crowded enclosure that created many physical constraints.
When deployed, the antenna was supported on the edge of the system's enclosure. In the stored and locked position, a shock system was designed to prevent the antenna from getting damaged while in transport.
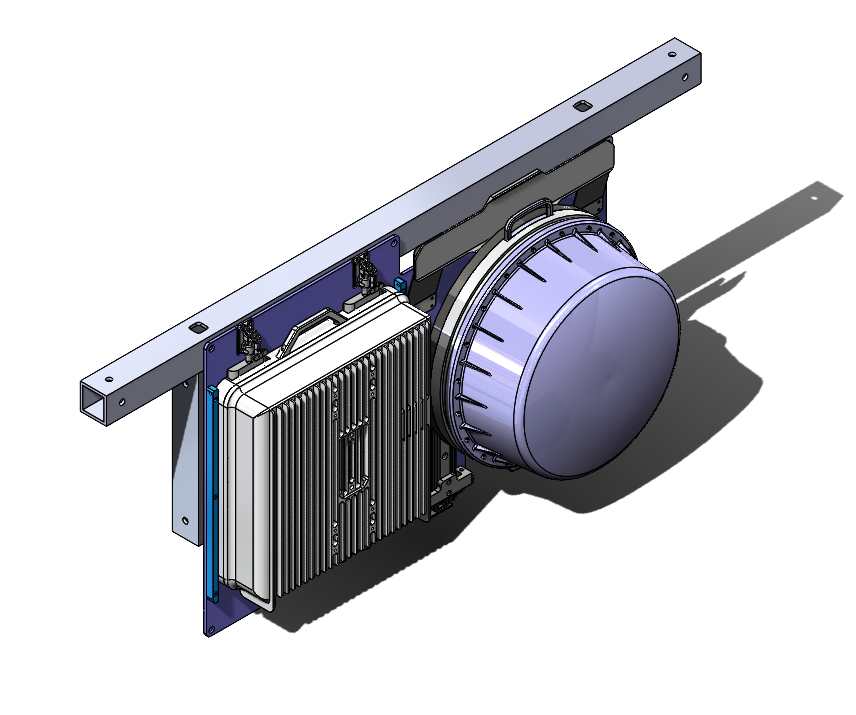
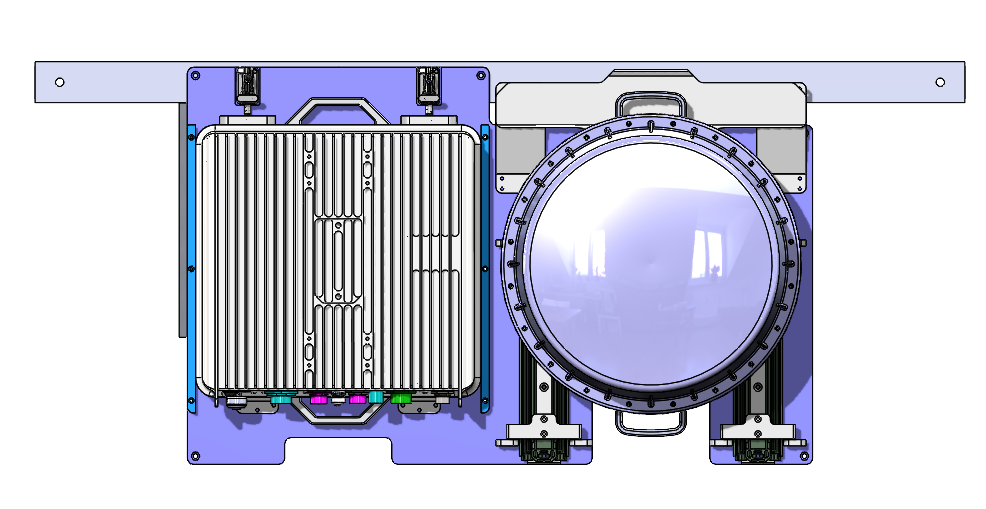
DUAL CAMERA MOUNT
~2021~
Designed a mount that housed a hefty thermal camera and smaller visible light camera in a ruggedized package attached to the top of a payload on a scissor lift meant to identify and track projectiles.
The shroud was made of fiberglass using a massive aluminum mold made in house. The visors were designed to be 3D printed, electronics were housed in a sealed box integrated into the mount, and the assembly was cooled with filtered fans.
The second iteration was created to be mounted on the side and have boresight capabilities. The new shroud was designed to be vacuumed formed and made the assembly much lighter.
This system was designed under tight size constraints, needing to be integrated into an existing assembly, and, ultimately, was not used due to changes to another subsystem.
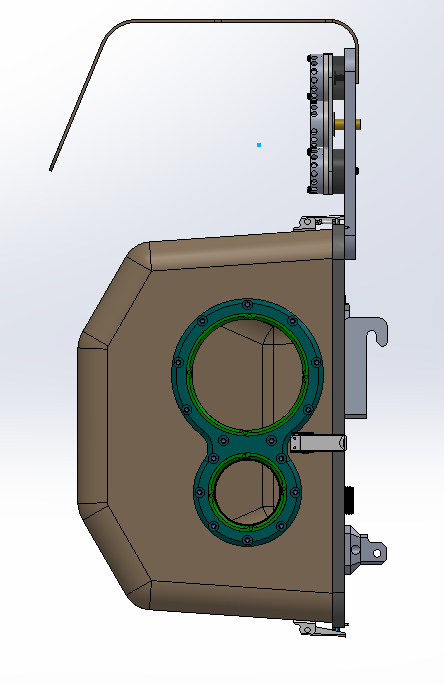
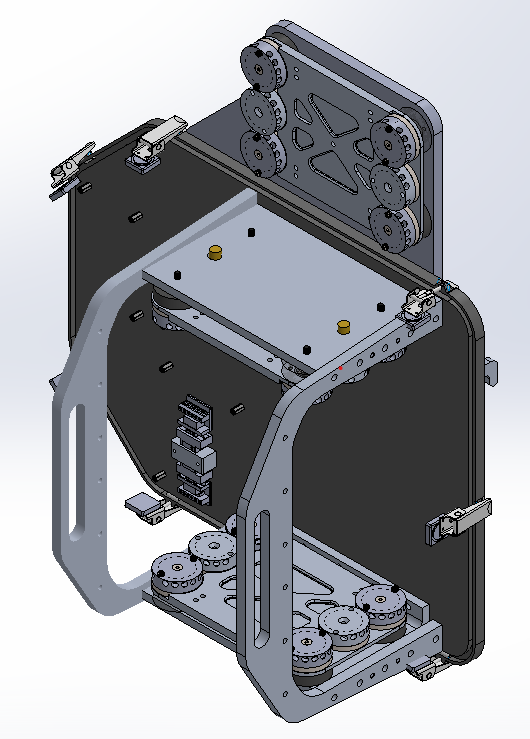
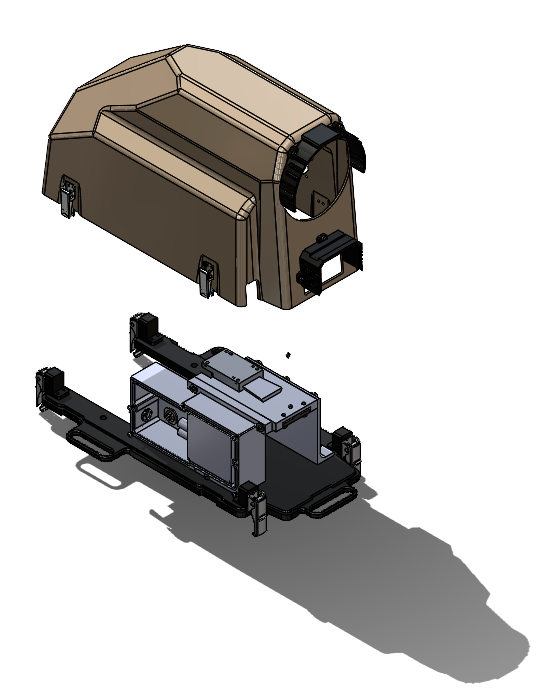
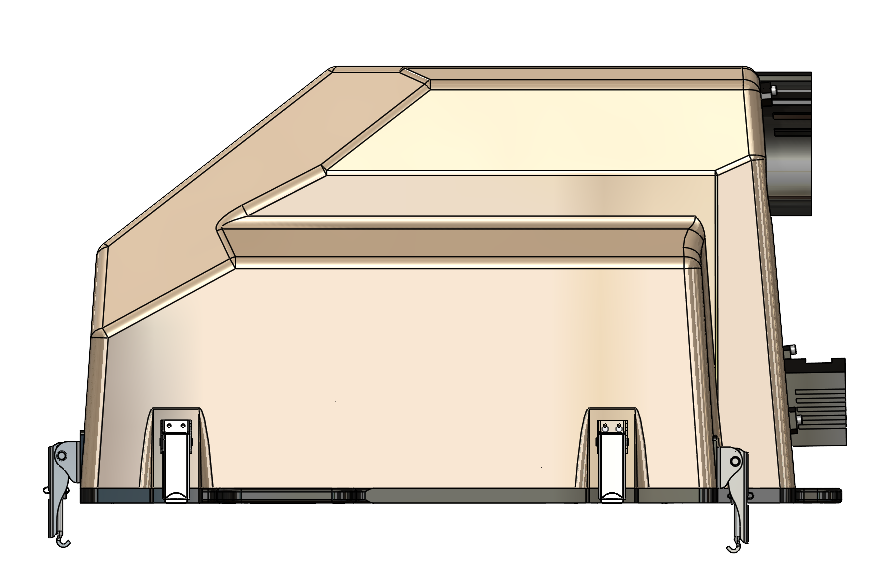
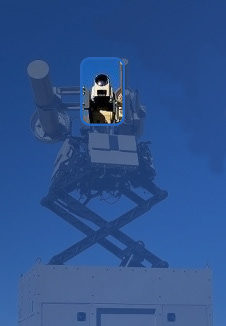
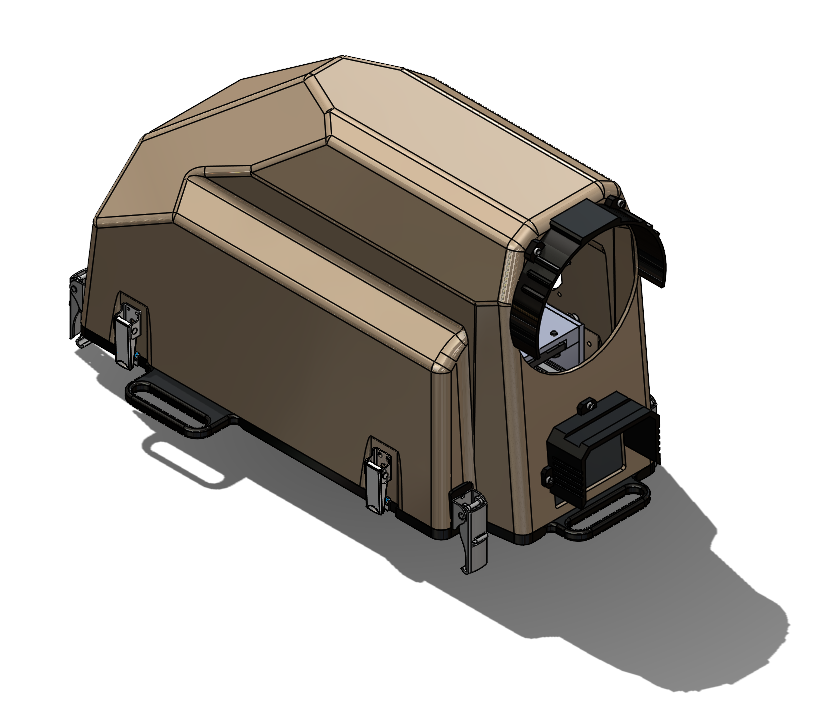
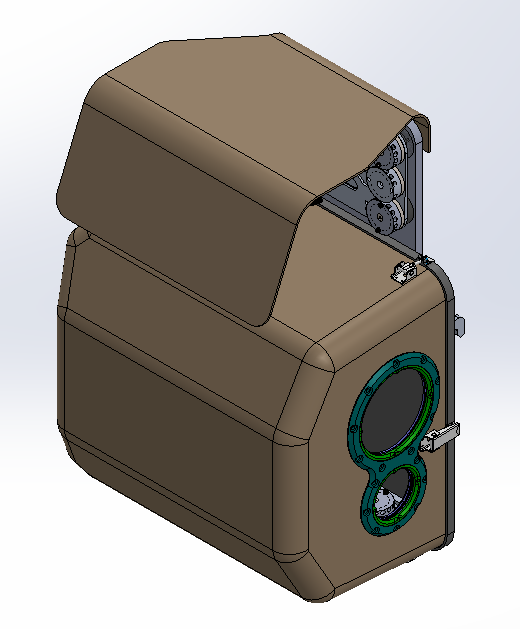
ELECTRONIC CABINETS
~2021- 2023~
Designed 4 generations of cabinets that housed various power and controls systems. Form and layouts of the cabinets needed to fit under tight size constraints but still allowing easy access for the user to wire and troubleshoot.
Later versions of the cabinets became modular, allowing the user to completely remove the system from an enclosure and get it replaced. Cabinets were designed to be rugged enough to withstand environmental conditions and rough user interaction.

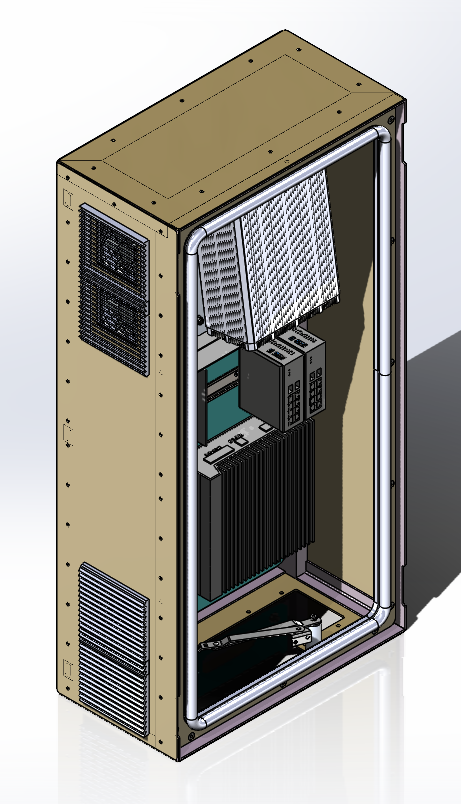
technical documentation examples
Examples of documentation skills through personal projects
LIGHTSABER CASE
~2022~
Skills:
- 3D Printing - 3D Modeling -
- Basic Circuits - Painting -
- Sewing -
During my most recent visit to Star Wars: Galaxy’s Edge, I had the pleasure of building my own lightsaber in Savi’s Workshop. After the long journey home, I stored the saber in the corner of my closet in the case that I left Disney with. This didn’t seem like a proper fate for my lovely saber, so I decided to replicate the beautiful cases that the Legacy Lightsabers come with for myself.
I modeled everything in SolidWorks and used hardware from McMaster Carr. I then printed it using my FDM printer and painted it. I pictured my lightsaber on a forest moon or Wookie-inhabited planet, so I chose to dirty it and paint it a darker green than the typical Legacy Lightsaber case. I also added lighting for an added effect.
For more info and pictures, go to 'Work' section of website!
THIS PROJECT WAS MADE FOR MYSELF AND MYSELF ONLY AND WILL NOT BE DISTRIBUTED.
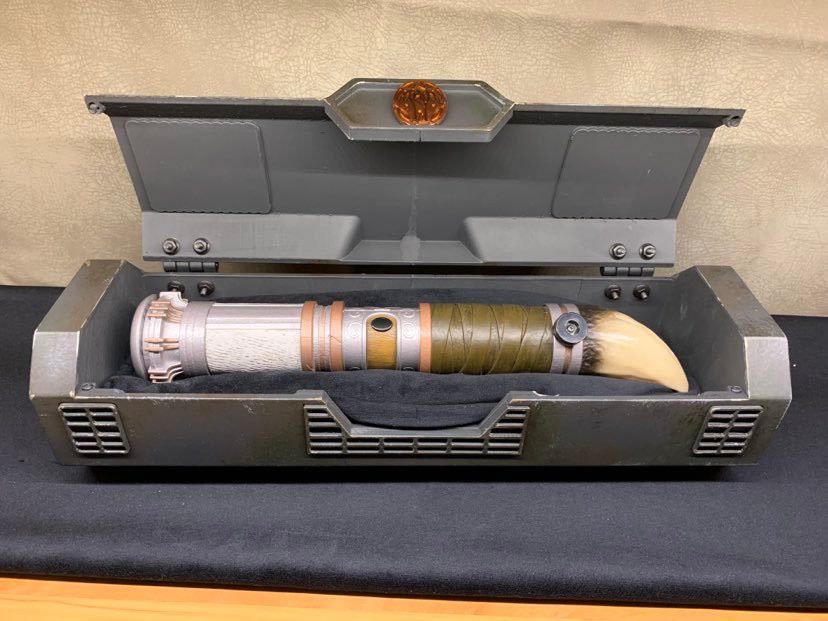
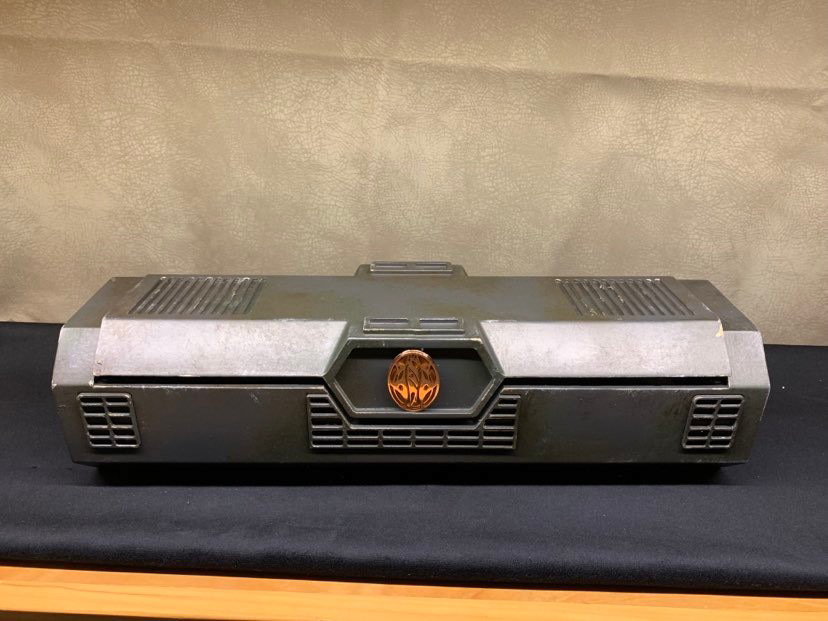
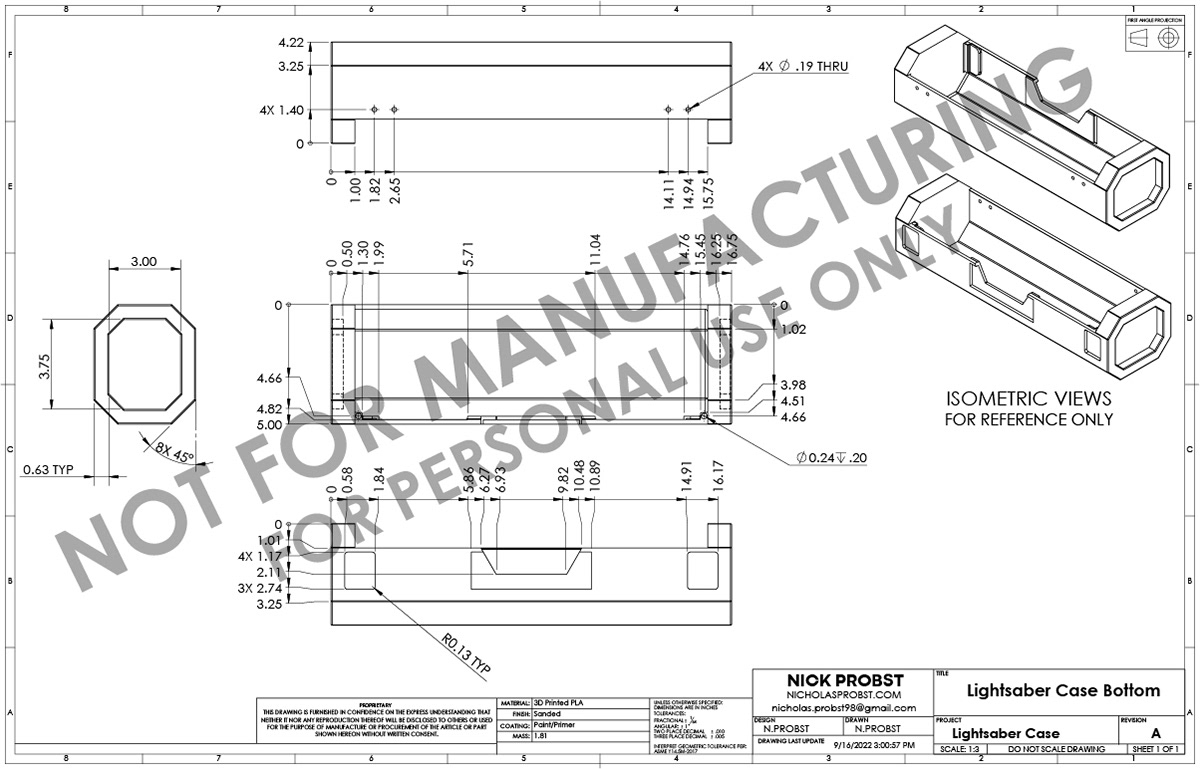
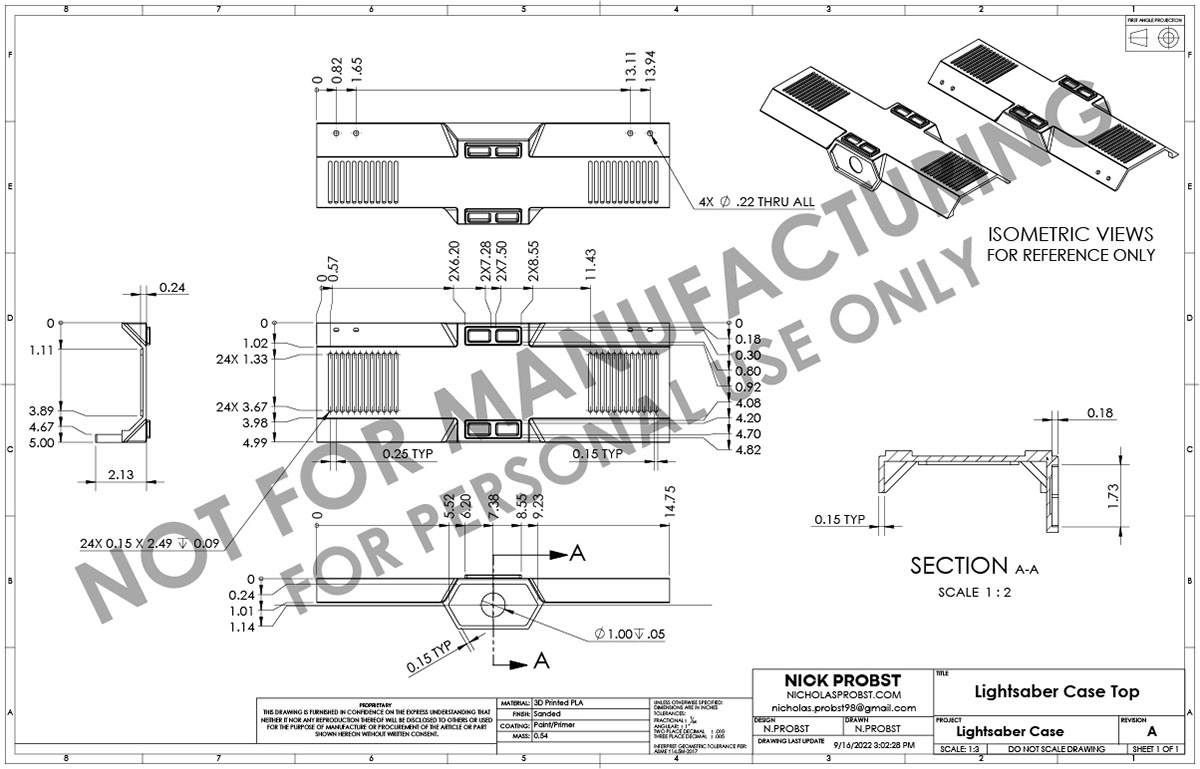
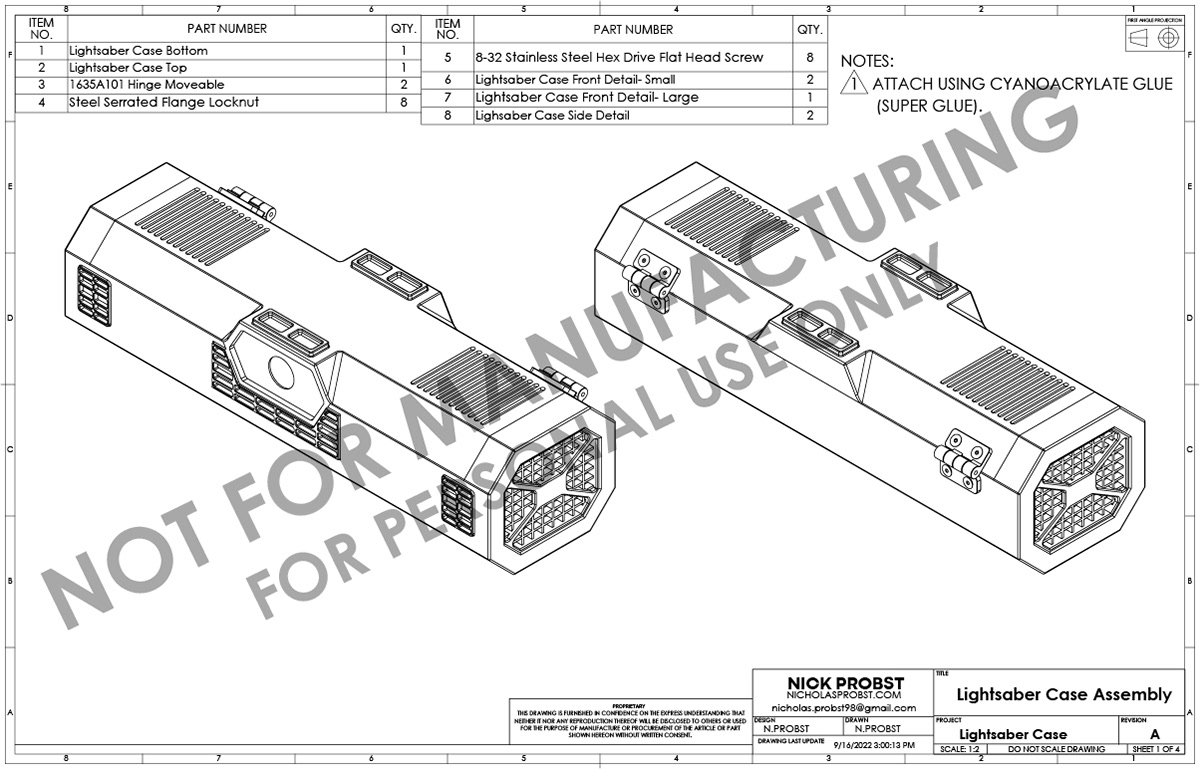
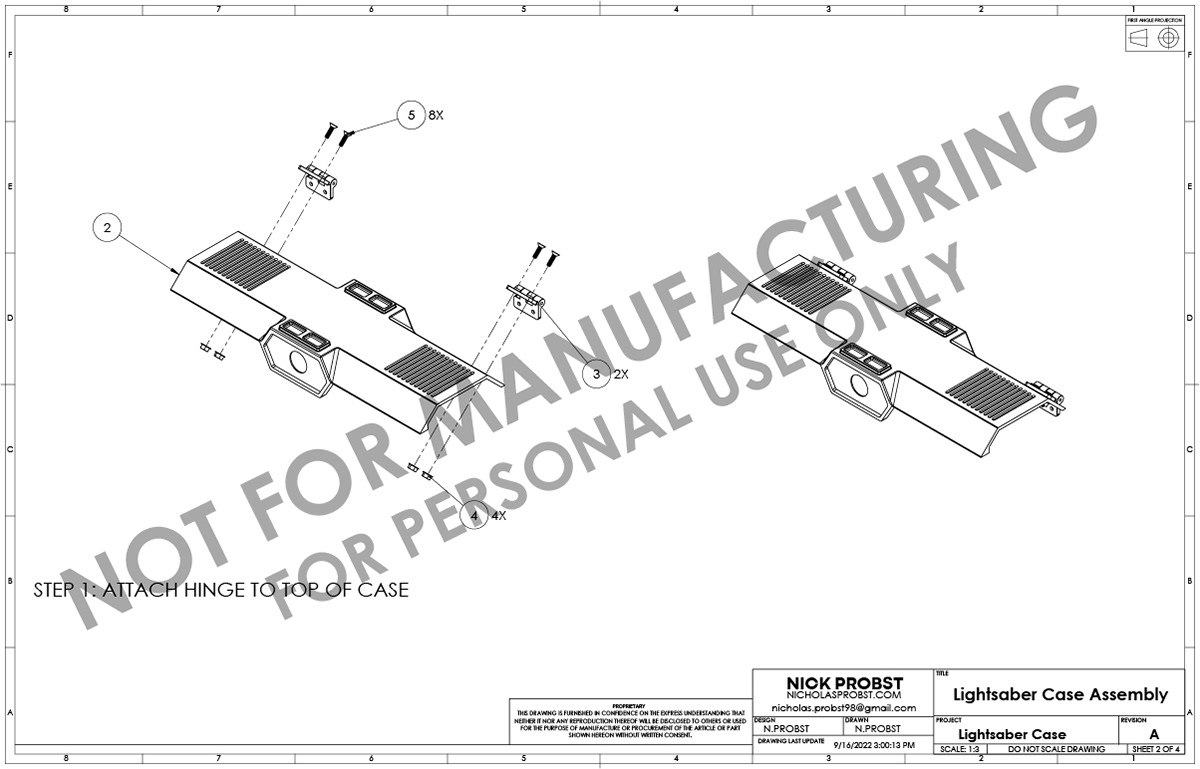
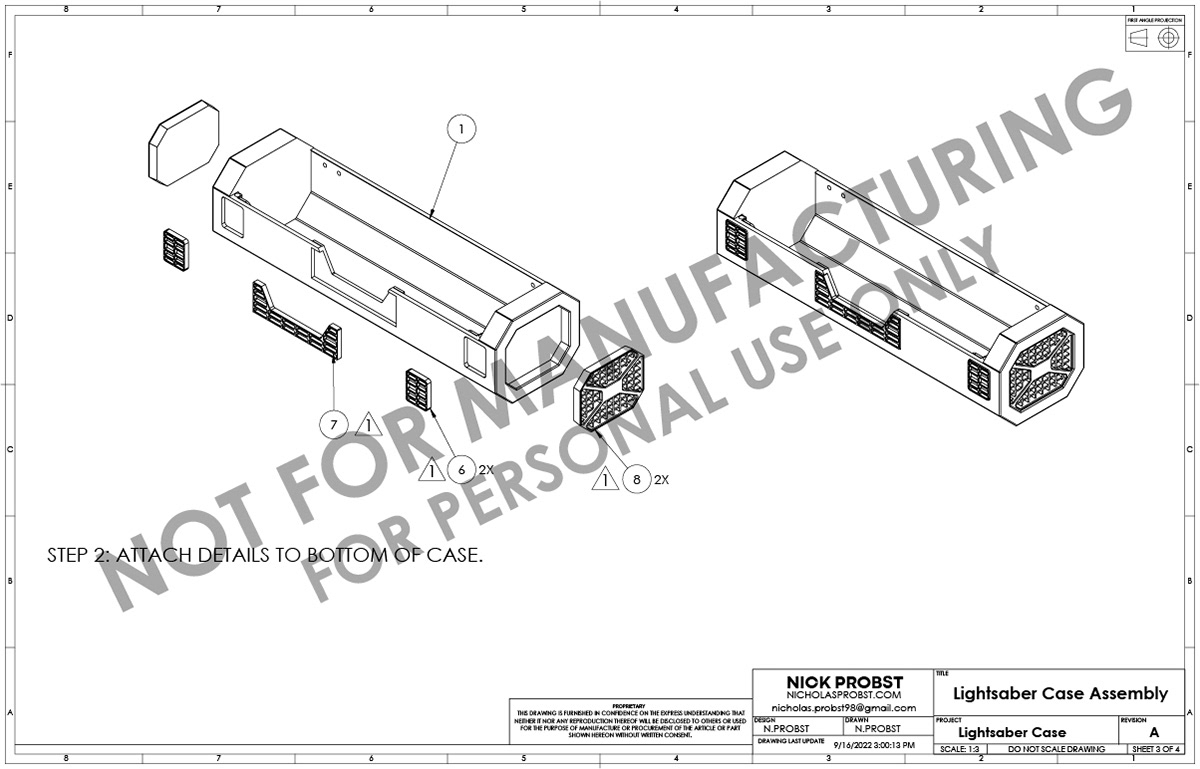
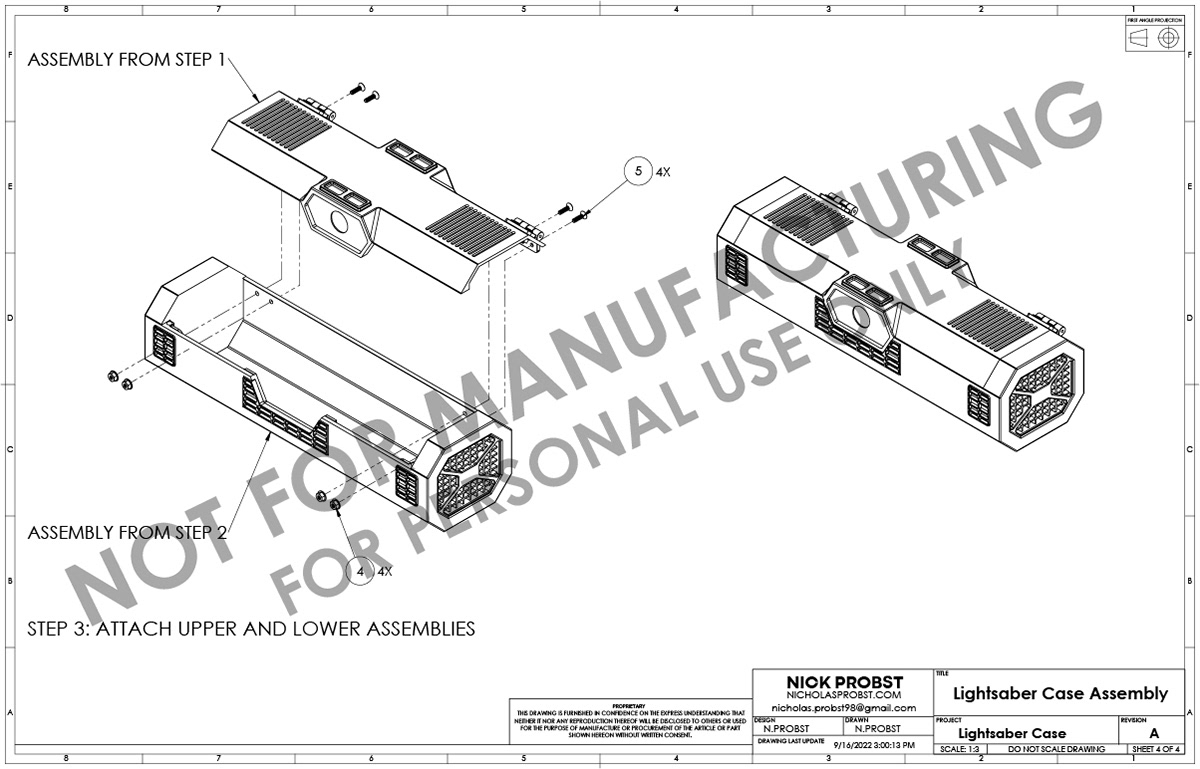
BLACK MANTA JET PACK TURBINE
~2021~
Skills:
- 3D Printing - 3D Modeling -
- Basic Circuits - Painting -
DC’s Aquaman had a villain that I have found to be one of the coolest looking in recent cinema. For Denver's Fan Expo, I made a replica of this costume. This was one of the most intensive 3D printing and modeling projects I have worked on.
Black Manta's iconic jet pack was made using both foam/thermoplastic and 3D printed parts. The details were printed and large parts were made of foam. Even with my precautions to use light materials, the jet pack was around 15 pounds. There was also a series of clear 3D printed parts that are positioned up the center of the jet pack. Each was outfitted with 20-25 LEDs to allow the jet pack to light up. I added two 'turbines' designed by myself that had motors to spin and create the effect from the movie.
I modeled everything in SolidWorks and used hardware from McMaster Carr. I then printed it using my FDM printer and attached it to the upper assembly. The purpose of this part is to hold a DC motor in the center of the 'turbine' and allow it to spin a fan I designed while still allowing air to be pushed into the jet pack to cool the electronics slightly.
For more info and pictures of this project, go to 'Work' section of website!
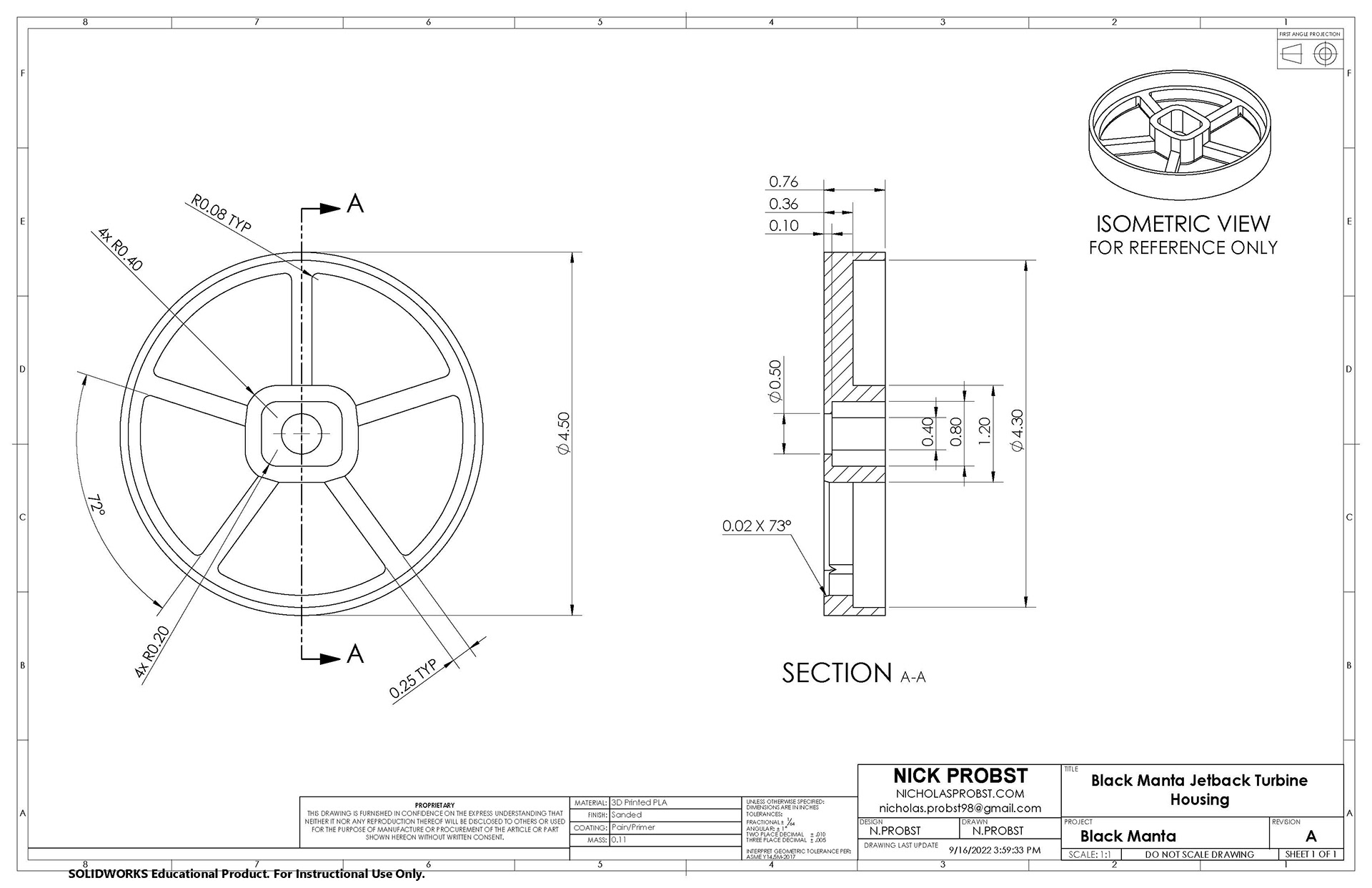
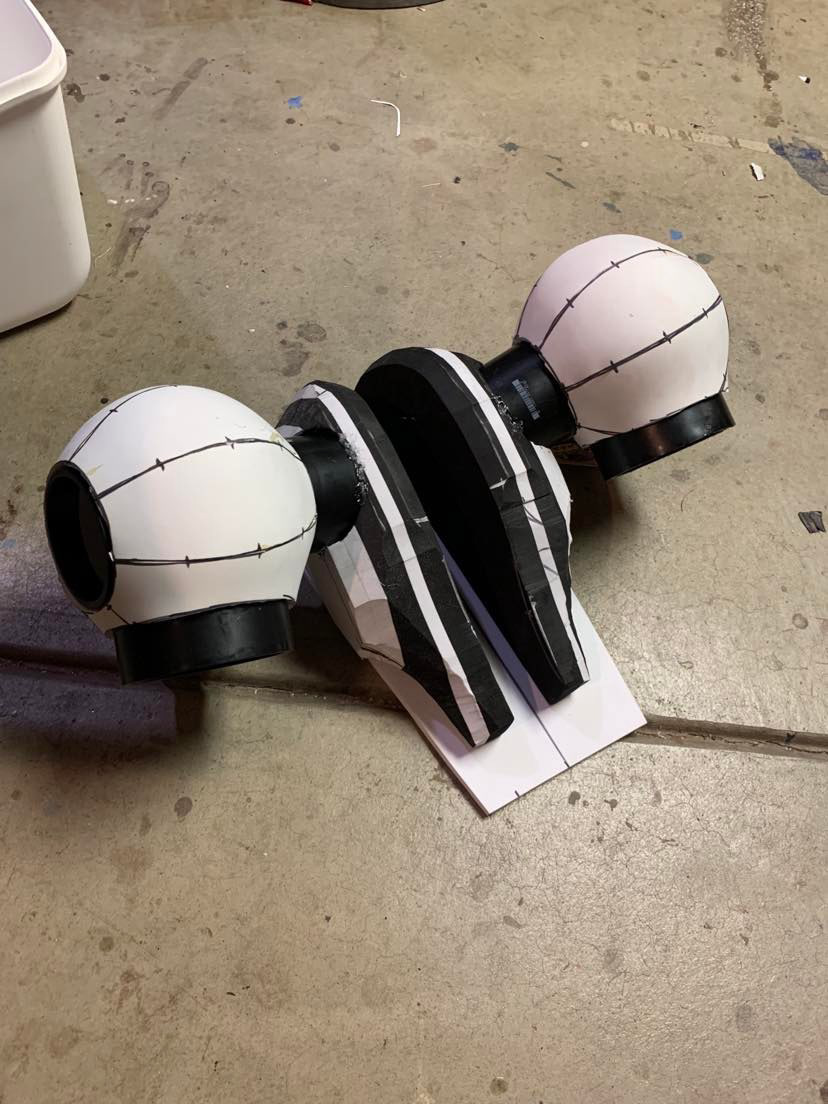
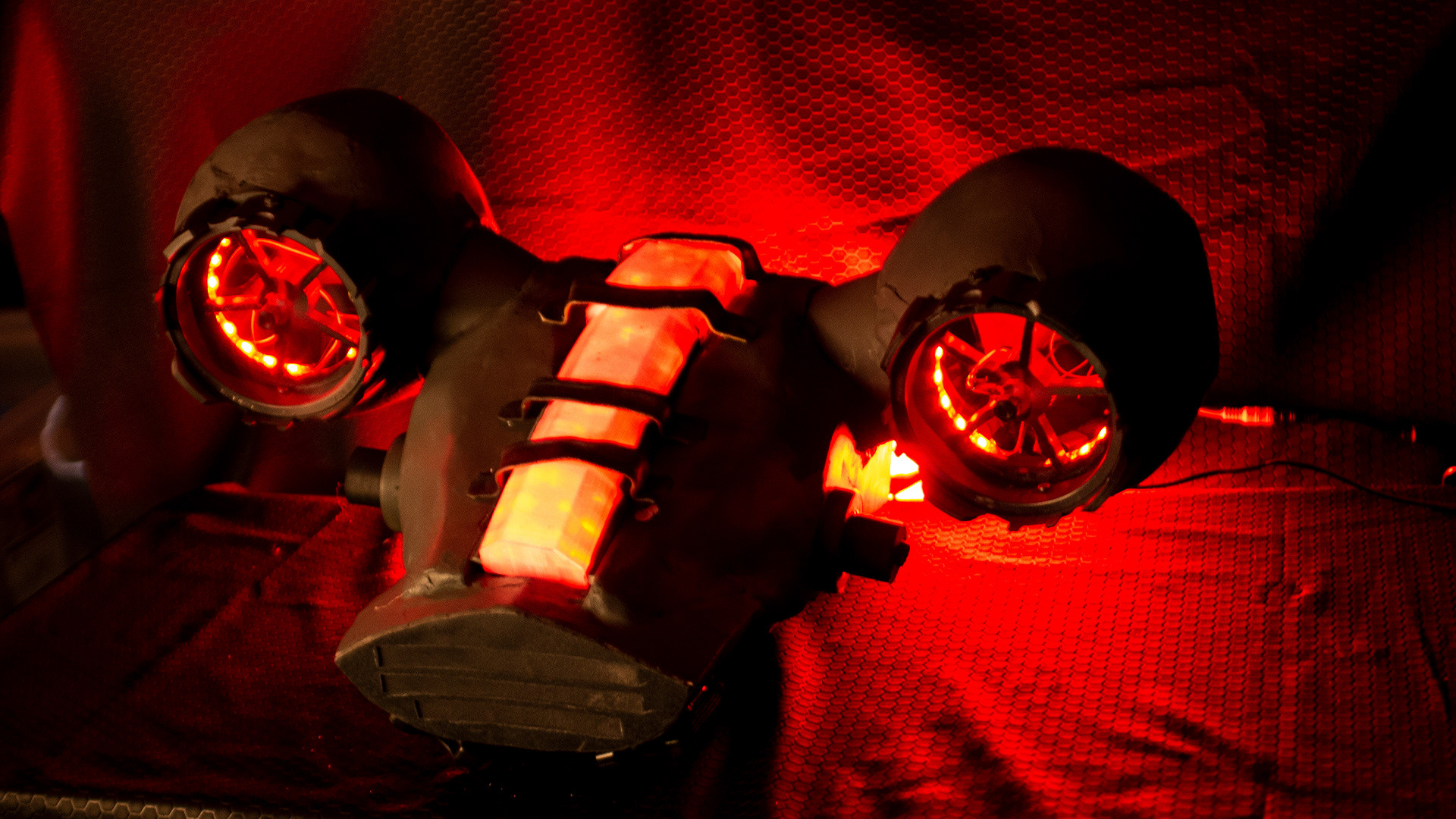